

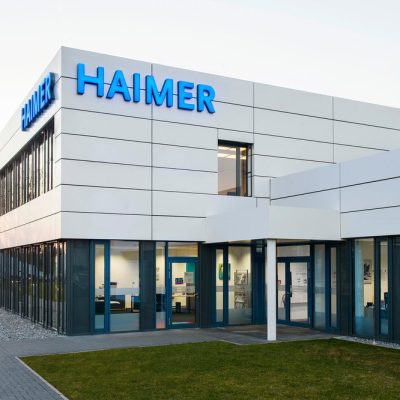
Pour réduire 250 tonnes de CO₂ chaque année, le groupe allemand Haimer, spécialisé dans la technologie de serrage d’outils, a consacré en 2023 plus d’un million d’euros dans des infrastructures respectueuses de l’environnement. Cas concret de durabilité.
Pour évaluer la durabilité, il ne faut pas se focaliser sur un produit, mais sur l’environnement, le cycle de vie du produit et l’ensemble du processus dans lequel le produit est intégré. L’usinage des métaux a de multiples aspects. Selon le matériau, la structure des éléments et les quantités, on utilise une grande diversité de machines, d’outils et de dispositifs de serrage. En plus des matériaux, l’efficacité énergétique joue un rôle essentiel dans la détermination d’un processus écologique. Une méthode prometteuse implique de cibler les consommateurs les plus importants et d’améliorer leur utilisation. La majorité de l’énergie utilisée dans l’usinage est consommée par la machine-outil, avec ses entraînements de broches et d’axes, ses périphériques et ses unités auxiliaires. Haimer a changé un centre d’usinage par un nouveau en utilisant le même procédé d’usinage, ce qui a entraîné une économie d’énergie de 30 %. Depuis plusieurs années, cette entreprise se sert exclusivement d’électricité issue des énergies renouvelables et investit dans des systèmes d’énergie solaire et des infrastructures respectueuses de l’environnement. Le processus d’usinage peut également être optimisé en utilisant des stratégies d’usinage optimisées par la CAO/FAO, telles que le fraisage trochoïdal.
En utilisant cette méthode, il est possible de diminuer le temps d’usinage de 71 minutes à 18 minutes par pièce en utilisant le fraisage trochoïdal avec les mandrins de frettage Haimer Power, par rapport à l’usinage avec une fraise à surfacer. La modification de la stratégie d’usinage a entraîné des économies d’énergie grâce à une consommation d’énergie considérablement réduite.
Durabilité du serrage des outils
De manière paradoxale, même un porte-outil peut jouer un rôle dans la durabilité ! Dans un processus d’usinage où la fraiseuse utilise en moyenne environ 30 kW, à laquelle s’ajoutent la puissance des dispositifs hydrauliques et pneumatiques, des équipements d’automatisation et des robots, on a tendance à croire que le porte-outil n’est qu’un élément secondaire. Le porte-outil est assez petit et le processus de serrage à l’aide d’un mandrin de frettage nécessite une consommation d’énergie marginale. D’autres systèmes de serrage consomment plus d’énergie lors du frettage qu’un mandrin hydraulique ou un mandrin de fraisage en utilisation opérationnelle.
Cycle de vie
Cependant, la situation évolue lorsque l’on considère l’ensemble du cycle de vie d’un porte-outil, qui englobe la fabrication, l’entretien et la décomposition. En raison de sa structure plus complexe, la fabrication d’un mandrin hydraulique nécessite beaucoup plus d’efforts et d’énergie. En plus de l’usinage de haute précision des divers éléments, il est nécessaire de souder le manchon d’expansion, de procéder à un traitement thermique supplémentaire afin d’éviter la rupture du joint de soudure, ainsi que tous les efforts pour le nettoyage, l’assemblage et le remplissage d’huile. Selon notre expérience, la quantité d’énergie requise pour la production est environ trois fois supérieure à celle requise pour le mandrin de frettage, explique Andreas Haimer, Directeur Général de Haimer GmbH.
Haimer a remplacé un centre d’usinage par un nouveau avec le même processus d’usinage, l’économie d’énergie était de 30 %.