
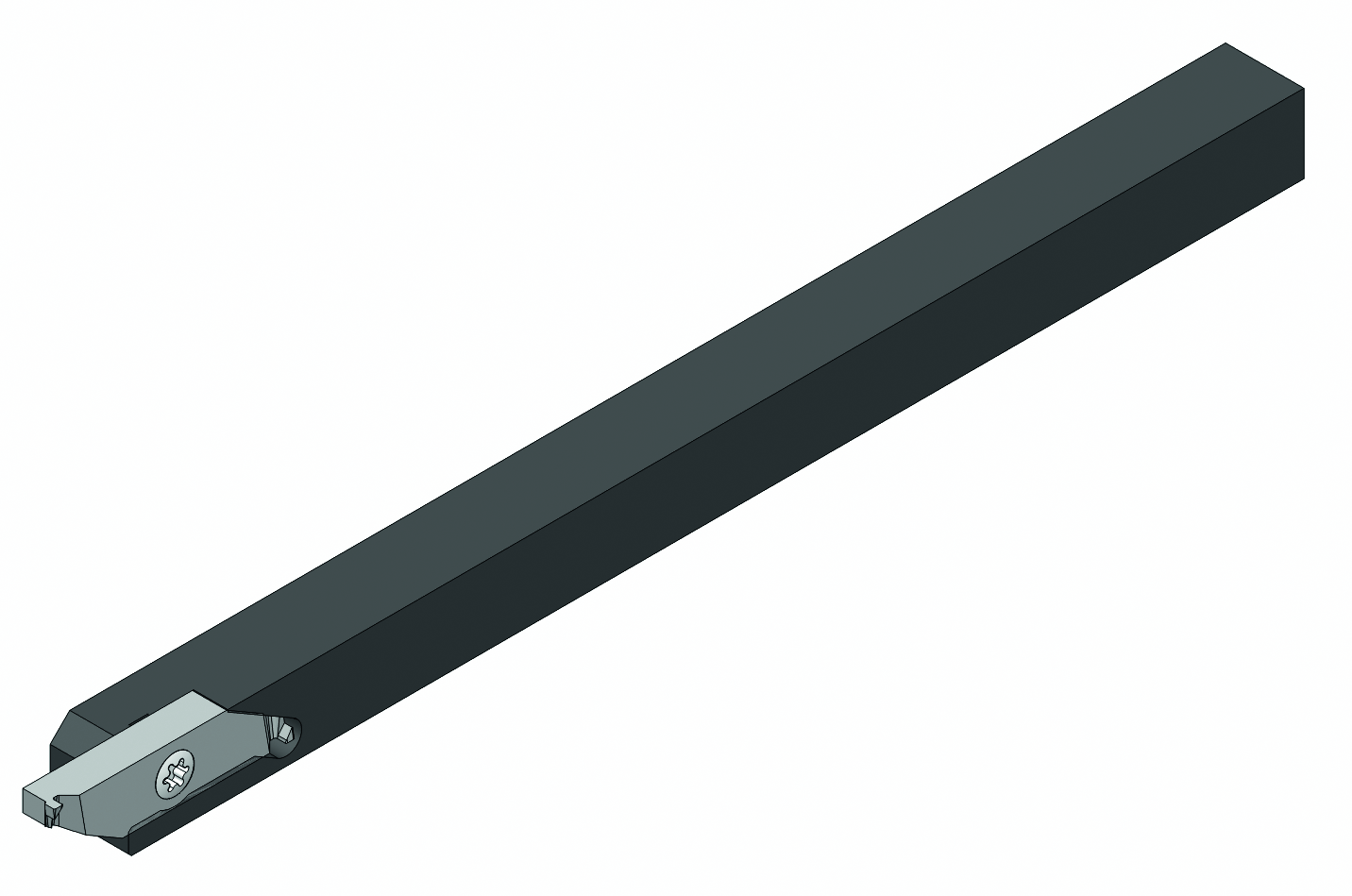
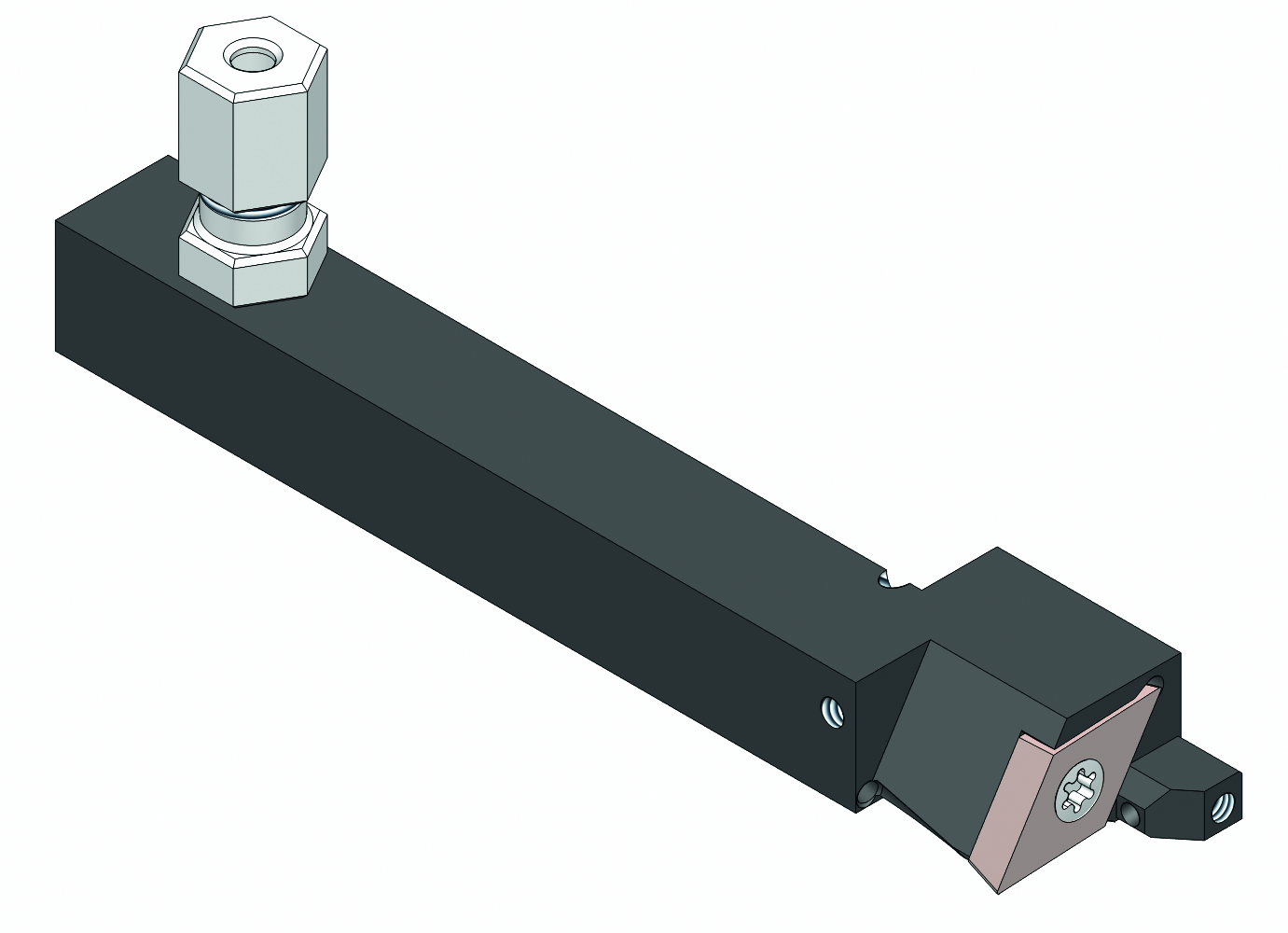
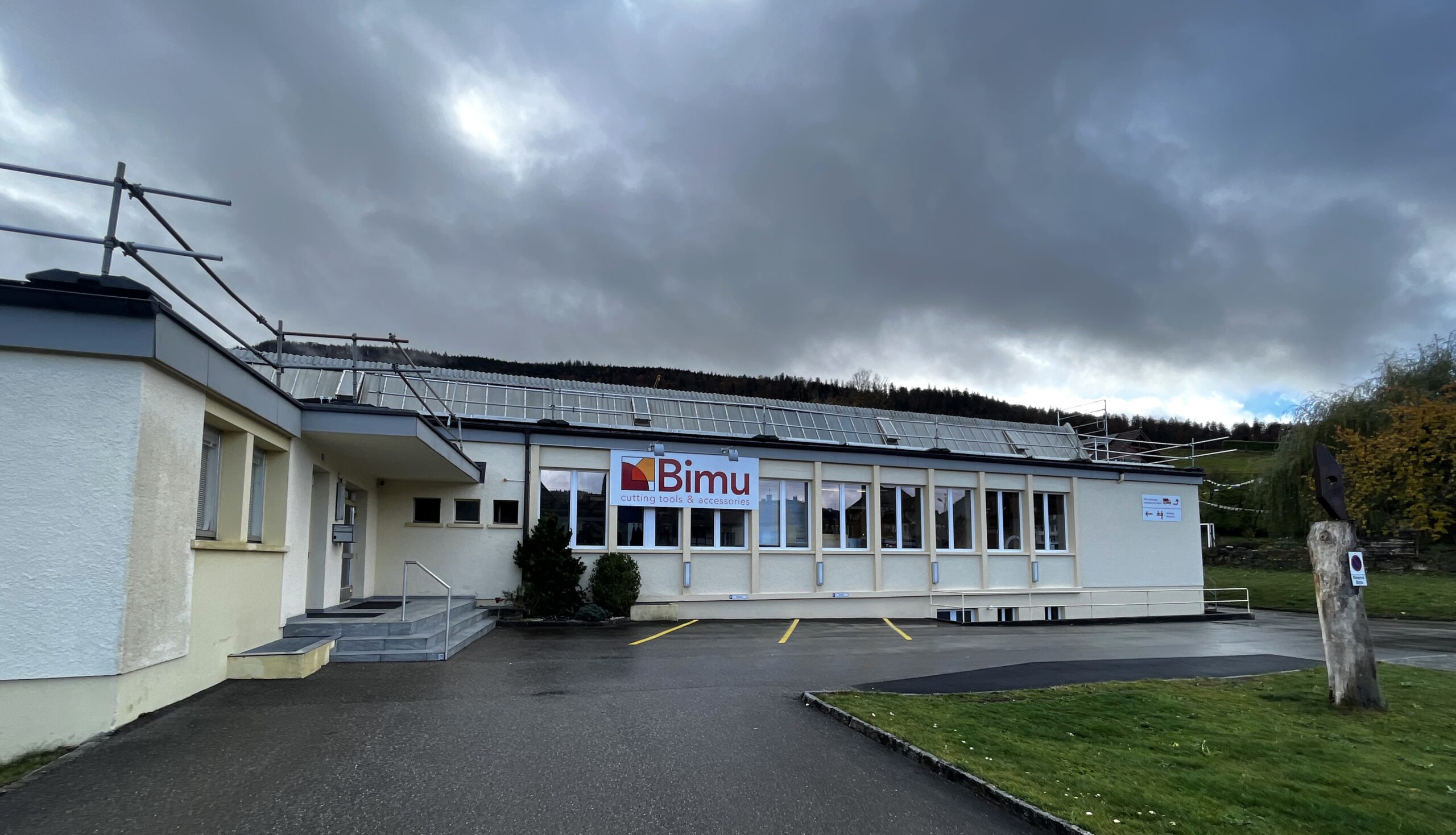
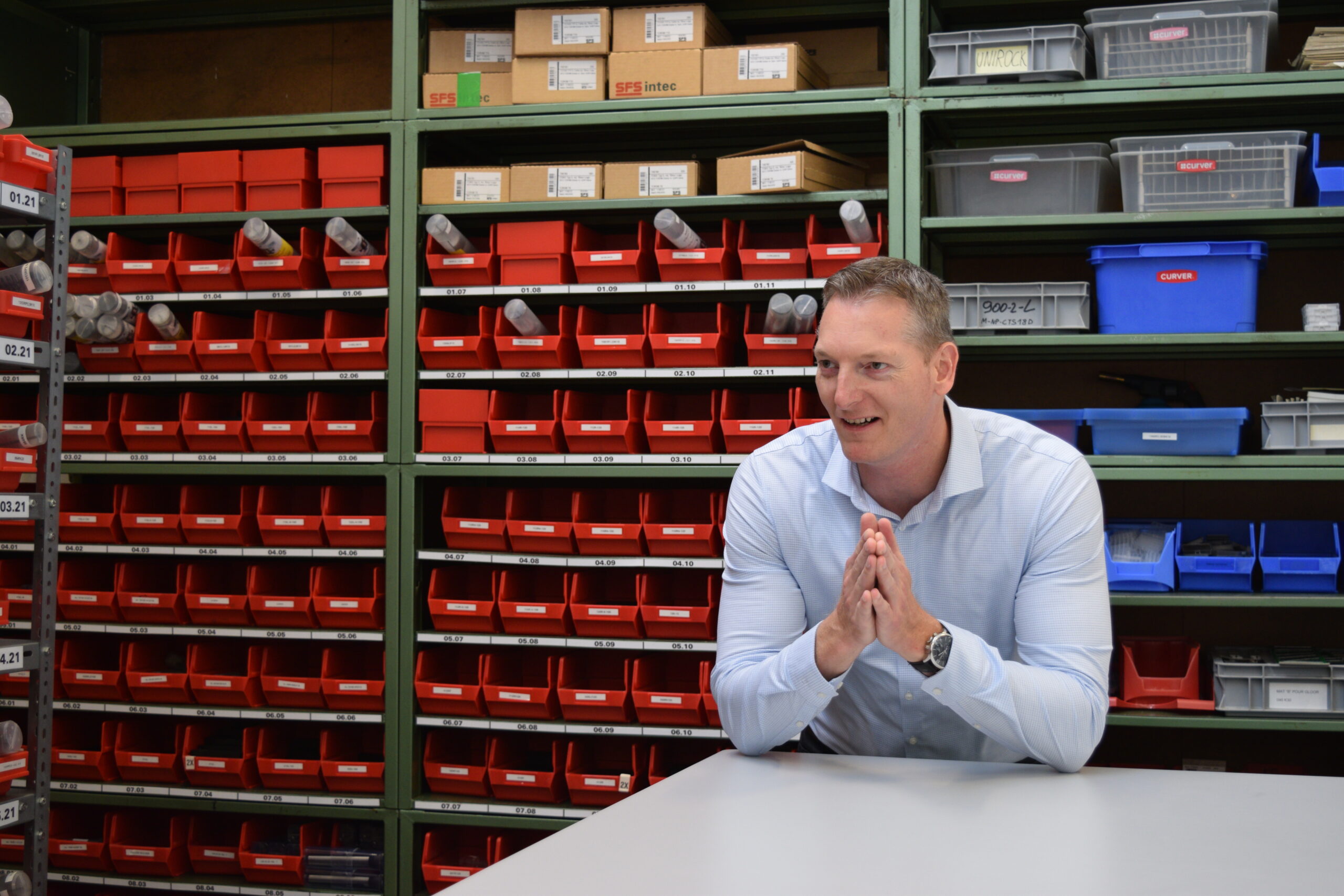
Dirigeant. Bimu, basée à Tavannes, Jura bernois, fabrique depuis plus de 25 ans de plaquettes de décolletage et d’accessoires pour tours automatiques. Son CEO Michael Zuber a repris l’entreprise après avoir multiplié les expériences. Mécanicien dans l’usinage à Bleienbach chez Langenthal, M. Zuber a travaillé dans le fraisage et tournage durant son apprentissage. Par la suite, il décroche son bachelor en ingénierie mécanique à la Haute école spécialisée bernoise (BFH). Une longue halte chez Dihart, comme ingénieur en développement, une autre chez Diametal en charge du réseau de revendeurs et Michael Zuber pose ses valises en 2017 chez Bimu et ses 22 employés.
Qui sont les clients de Bimu SA ?
En Suisse, nos clients opèrent dans l’horlogerie et dans le médical. Ces deux secteurs sont les piliers de Bimu. Nous fournissons aux décolleteurs les outils de coupe. Nous fabriquons uniquement des plaquettes de décolletage en métal dur, des porte-outils, des systèmes à changement rapide ainsi que d’autres accessoires pour tours automatiques à poupée mobile. Nos plaquettes sont conçues pour le tournage extérieur. Nous faisons 70% à l’exportation notamment vers l’Allemagne, l’Espagne, la Chine, la Thaïlande et autres. Les marchés varient selon les secteurs. Ainsi, la Corée du Sud utilise nos plaquettes pour les produits médicaux et les implants dentaires, l’Allemagne pour l’automobile et la sous-traitance de cette industrie. Le diamètre de tournage est souvent plus grand. La Suisse représente 30% de notre chiffre d’affaires. Bimu produit à Tavannes environ 450’000 plaquettes en métal dur par année. Lorsque nous faisons une nouvelle géométrie de plaquette nous la publions sur notre site web.
L’utilisation de nouveaux matériaux sur le marché exige des adaptations au niveau des outils. Comment fait Bimu pour rester en permanence dans la course ?
Pour les nouveaux matériaux, le défi commence chez notre client final. Il exprime son souhait d’usiner des aciers inox qui sont plus résistants à l’oxydation, donc composés d’autres alliages. Si la matière devient plus difficile à usiner, pas forcément plus dure, les outils de coupe, leurs géométries et le revêtement devront suivre et être adaptés pour cet usinage. Face à de nouvelles matières, nous testons avec le client différentes géométries, différentes préparations d’arêtes avec des revêtements résistants à la chaleur ou très lisses, etc… Nous faisons tous ces tests et nous créons une gamme d’outils spécifiques. Si la demande est récurrente, Bimu peut créer une gamme d’outils standard pour cette nouvelle matière. Souvent Bimu ne reçoit pas le nouvel alliage car il est très cher et donc le client teste l’outil chez lui. Le laiton sans plomb est, par exemple, un tout nouveau classique.
Concernant le laiton sans plomb, des progrès considérables peuvent être encore réalisés dans le développement des outils de coupe ? Un mot sur ces avancées ?
Dans l’horlogerie tout comme dans la connectique, les clients doivent éviter le plomb pour des raisons de santé et d’environnement. Le plomb facilite l’usinage et reste meilleur marché. Les fonderies ont commencé à faire des alliages sans plomb. Tout le monde a essayé d’usiner le laiton sans plomb avec les outils existants et nous avons constaté que c’était un échec. Les copaux forment des fils, des nids d’oiseaux qui abiment la pièce finie. Bimu a développé des géométries et des revêtements très lisses qui maitrisent mieux les copeaux. Les revêtements de nos outils sont faits à l’externe en Suisse. Nous achetons les ébauches en métal dur. Chez Bimu, la valeur ajoutée réside dans le meulage et la conception des porte-outils. Aujourd’hui, les gros fournisseurs d’outils ont un département qui fait les revêtements mais ils ont aussi une partie qui est sous-traitée car l’innovation technologique s’effectue très souvent à l’externe par des entreprises spécialisées en traitements de surface. L’année prochaine, nous lancerons une nouvelle géométrie qui a fait ses preuves en interne pour usiner le laiton sans plomb.
Pour ce qui est de briser les copeaux, quelles sont les améliorations des derniers mois chez Bimu ?
Bimu excelle dans ce domaine. Nous faisons la différence entre briser les copeaux et les rouler. Pour certaines matières, les géométries de coupe ont plutôt tendance à briser les copeaux. C’est notamment le cas avec le cuivre qui est très tendre et pour lequel il est judicieux de contrôler le copeau en le cassant juste après sa formation, permettant ainsi de le faire tomber immédiatement. Ceci évite ainsi la formation de nids de copeaux.
Le tournage de toutes petites pièces dans le domaine extérieur a encore du potentiel. Allez-vous rechercher des partenaires commerciaux adéquats ?
En Suisse, nos quatre vendeurs sont en permanence sur la route. Je cherche des revendeurs dans les pays dans lesquels il y a un marché du décolletage. Actuellement je suis en contact avec un revendeur en Finlande, un deuxième en Inde et un autre aux États-Unis. Notre rapport qualité-prix est très élevé. En contrepartie, la qualité est synonyme de durée de vie de l’outil. Si un client produit cinq mille pièces, avec le même process, nous lui proposerons un outil qui doublera sa production. Finalement, le client sera gagnant même avec un prix d’outil légèrement plus cher. Une plaquette coûte en moyenne vingt francs. L’ébauche oscille entre deux et trois francs, le revêtement un franc. Cela étant, notre valeur ajoutée se niche dans le meulage. Au niveau prix en Suisse, nous sommes les moins chers. Avec le meulage et nos process, nous fabriquons des outils de haute qualité avec une durée de vie supérieure.
Bimu a développé des géométries et des revêtements lisses qui maitrisent mieux les copeaux.
La maitrise des six axes
Bimu souffre de la pénurie de personnel qualifié. Elle est en quête permanente de compétences capables de programmer une machine avec cinq ou six axes. Des polymécaniciens spécialisés dans le meulage sont déjà rares sur le marché, mais peu sont rompus aux machines Rollomatic. En fait, il faut une année de formation chez Bimu sur les Rollomatic pour maitriser les six axes. C’est du learning by doing sous la houlette du chef d’atelier.